We’ve been working on the BlueRobotics Thruster-100 for almost nine months now. It started as a side project to replicate a commercial grade thruster but evolved into much more. We think it would be cool to share some of that process. This first post shows the evolution of the thruster design from day one until now.
We started by trying to replicate the “industry standard” commercial thruster design, which is essentially a motor sealed in a tube. A shaft extends from the end of the tube to attach to the propeller and a nozzle protects the propeller and increases the thrust. There’s several ways to create a sealed shaft: you can use sealed bearings with grease or you can use a magnetic coupling. Our first four design revisions used magnetic couplings to link the motor to the propeller through a watertight seal. Inside the tube, the magnetic coupling attached to an RC airplane brushless motor.
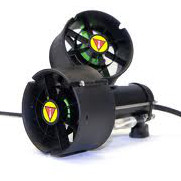
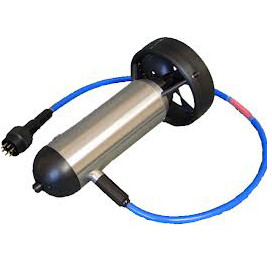
A few examples of commercial thrusters that inspired our original design.
We stuck with this design for our first four revisions but we ran into a lot of trouble. They had sensitive tolerances, expensive parts, and we needed steel ball bearings that would corrode in saltwater. We also had trouble finding an off-the-shelf brushless motor that had the high torque and low speed needed for a marine propeller.
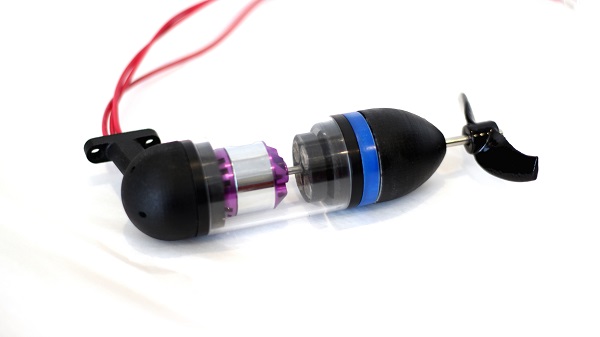
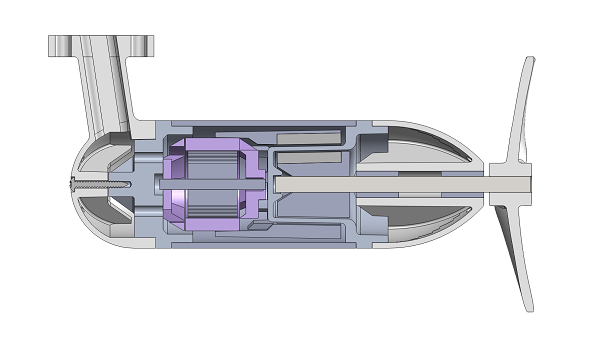
Our first prototype, mostly hand machined on a lathe (left) and a section view of our Revision 4 design, showing the motor and radial magnetic coupling (right).
We decided that we needed to build our own brushless motor – one that had high torque and was very efficient. We built a number of test motors with different stators, windings, and magnets to find one that worked well underwater. In the process we imagined our current thruster design. Here is the entire evolution of the thruster design from day one until now.
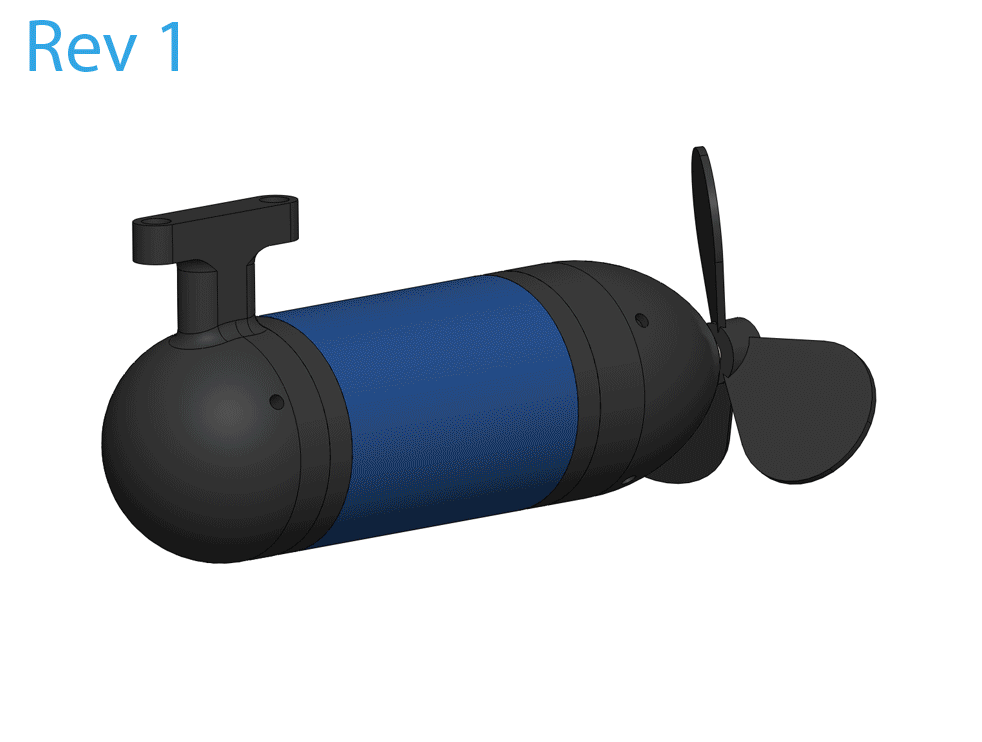
What makes the new design different? It gets rid of the tube, seals, and couplings. Instead of sealing the motor in a tube, each part of the motor is sealed with a protective coating and the bearings are high-performance plastic. When running, water flows freely through the motor but it’s protected from short circuits and corrosion. Injection molded plastic parts from Proto Labs form the structure of the motor. It was a dramatic change from our starting point but it results in an affordable, high-performance thruster. For more info about the thruster design, check out the thruster page.