Fighting Galvanic Corrosion with Zinc and Tef-Gel
Galvanic corrosion is the electrochemical process that occurs when two dissimilar metals are immersed in a conductive solution, like saltwater. The rate and severity of the reaction is determined by the Galvanic Series, which describes the magnitude of the voltage potential between different metals. You can see the spectrum of potential in this chart:
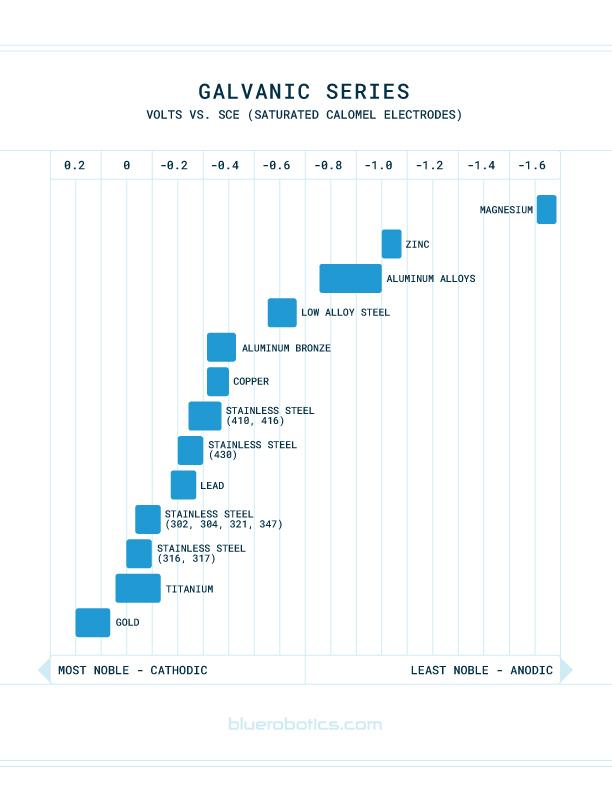
Blue Robotics Watertight Enclosures and Watertight Boxes use a combination of aluminum parts with stainless steel hardware. While stainless steel and aluminum are both wonderful metals for use in the marine environment, when used in close proximity to one another, a potential voltage difference of 0.5 to 1 V can drive the aluminum to corrode.
Galvanic corrosion isn’t much of a concern during short-term submersion, but during long-term deployments of many weeks at a time or more, its effects can cause some problems. This guide details how Blue Robotics watertight enclosures and boxes can be protected from the effects of galvanic corrosion during long-term submersion through a combination of anticorrosive lubricant and use of a sacrificial anode.
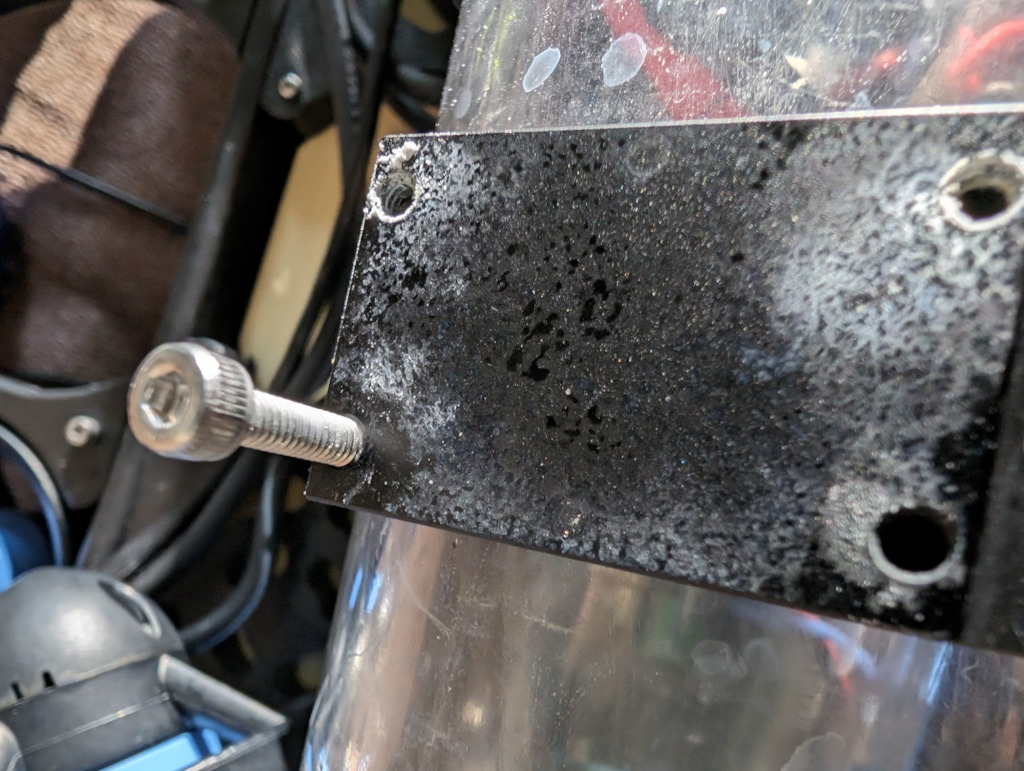
Powdery residue, aluminum oxide, from galvanic corrosion between the stainless steel bolt and the aluminum watertight enclosure clamp
Using Tef-Gel
Tef-Gel is an anti-corrosion and anti-seize lubricant that does a remarkable job at preventing contact between dissimilar metals. It is commonly applied to rivets on sailboat masts to prevent galvanic corrosion. Applying Tef-Gel to a bolt’s threads nearly completely electrically isolates the bolt from the material into which it is threaded. This isolation creates high resistance between the metals, impeding the galvanic series voltage difference that drives corrosion and thus reducing the rate of corrosion.
To use Tef-Gel, coat all stainless steel surfaces that will contact aluminum, such as the bolts securing end caps to O-ring flanges. Just coat the bolt’s threads with Tef-Gel, or optionally, smudge some on the top of the threaded holes. Then, tighten the bolt as usual, being careful not to strip the aluminum threads. You can perform this application on both our cylindrical watertight enclosure flanges and our watertight box enclosures, or any other aluminum hardware!
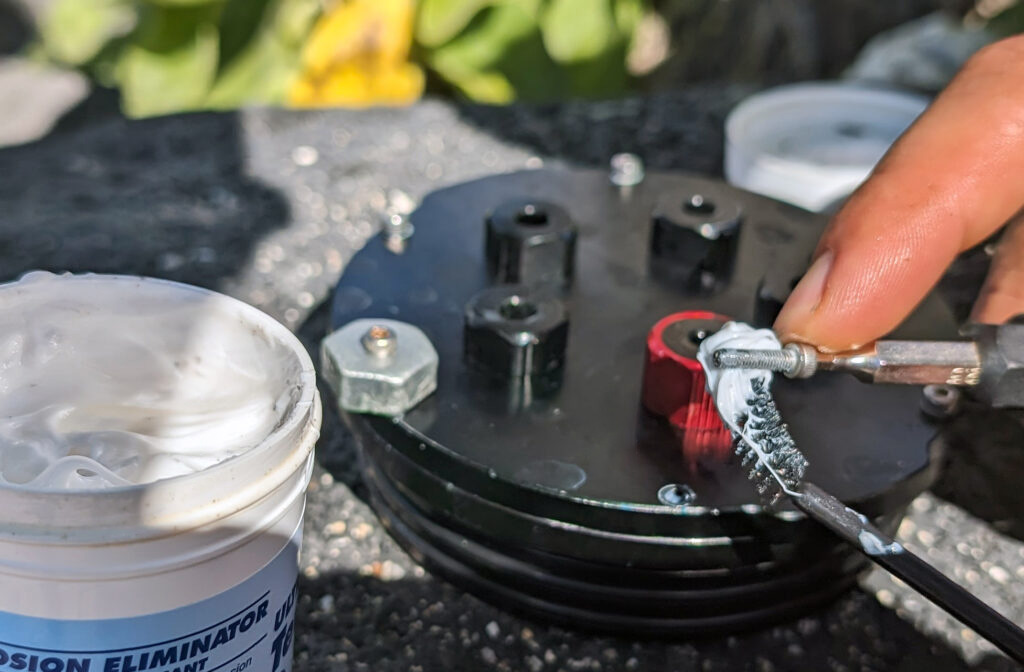
Don't be shy with the amount of Tef-Gel used, and don’t expose it to temperatures above 450F/230C!
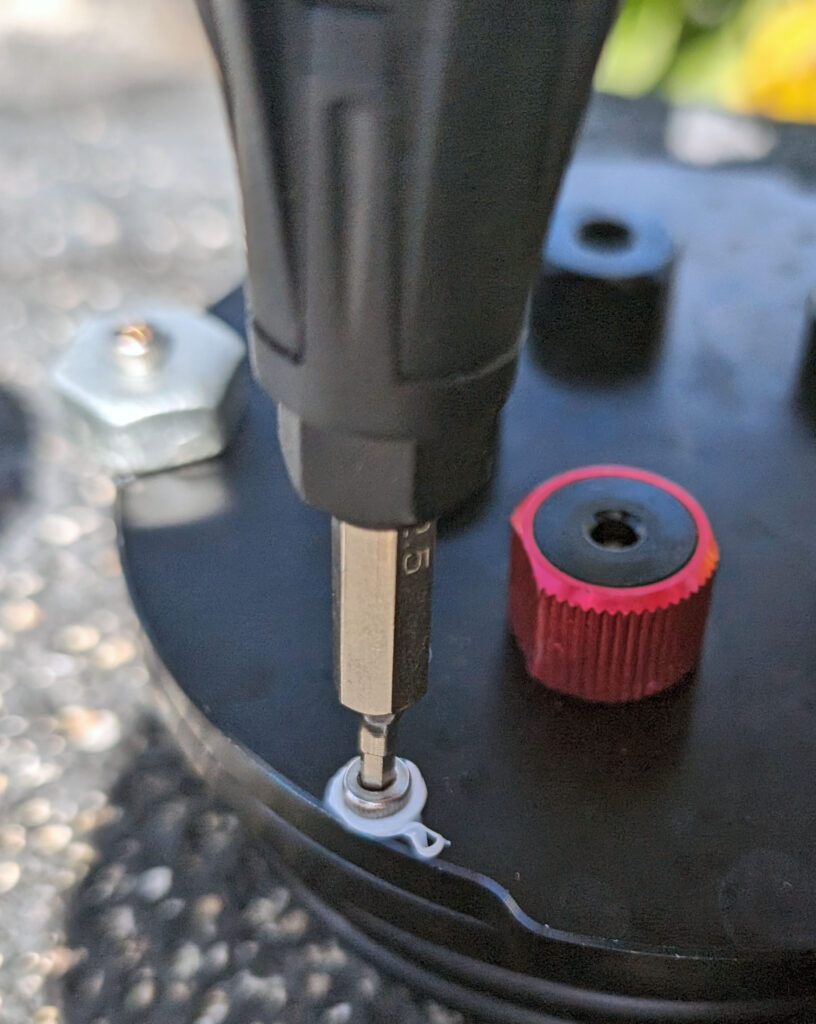
Using Zinc as a Sacrificial Anode
A sacrificial anode is a metal piece used to prevent corrosion in other metals by corroding first, taking the damage instead of the parts you want to protect. Zinc metal, possessing a higher potential voltage in the galvanic series, corrodes instead of aluminum, acting as a the sacrificial anode. Over time, the zinc will erode away completely! If you plan to submerge your BlueROV2 or enclosure for long, continuous periods, installing sacrificial anodes will help prevent corrosion of aluminum.
For resident ROV applications, where an ROV is permanently or semi-permanently stationed underwater, this is crucial since power-over-tether systems and strong water currents it may experience can accelerate galvanic corrosion!
To provide corrosion benefits, the zinc anode needs to be electrically connected to both the aluminum and stainless steel in order to protect both metals. When using with our cylindrical watertight enclosures, at least one zinc anode attached to each O-ring flange will protect the associated hardware, including any penetrators or connectors used on the end cap plate. For water tight boxes, you may want one zinc anode for the box and one for its lid.
To install a chunk of zinc, drill a hole through its center that fits the fastener size you plan to use for attachment. Since the recommended anode‘s thickness is just under 8mm, ensure the bolt you choose extends at least 5 mm beyond the standard length for that particular spot. If you opt for a different zinc anode, verify that your bolt can accommodate its thickness! Attach the zinc by placing it between the stainless steel bolt’s head and the aluminum.
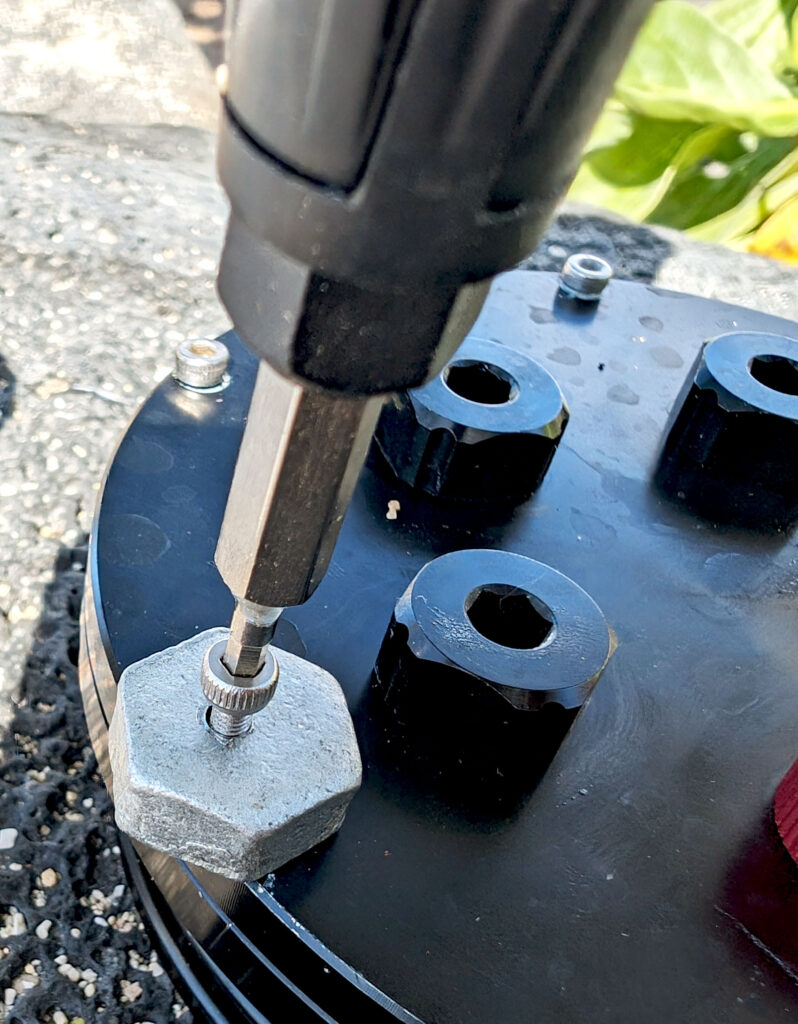
As the zinc deteriorates and shrinks over time, the bolt fastening it may exert less clamping force on the O-ring face-seal in watertight enclosure endcap/flange applications. Fortunately, external pressure at even minimal depths keeps the face-seal engaged! You don’t need to remove the hardware from water to periodically tighten the bolt. However, maintaining a tight connection ensures continuous electrical contact, preserving a consistent level of protection.
The aluminum tube in a watertight enclosure is isolated from any contact with stainless steel by the rubber O-rings, and should not need protection. Wrapping them in electrical tape can help preserve the anodized coating in long deployments.
Results
While we’ve not conducted formal testing, we’ve seen this technique used with our 3″ watertight enclosure in camera deployments in aquaculture, as well as resident BlueROV2 units, with dramatic results!
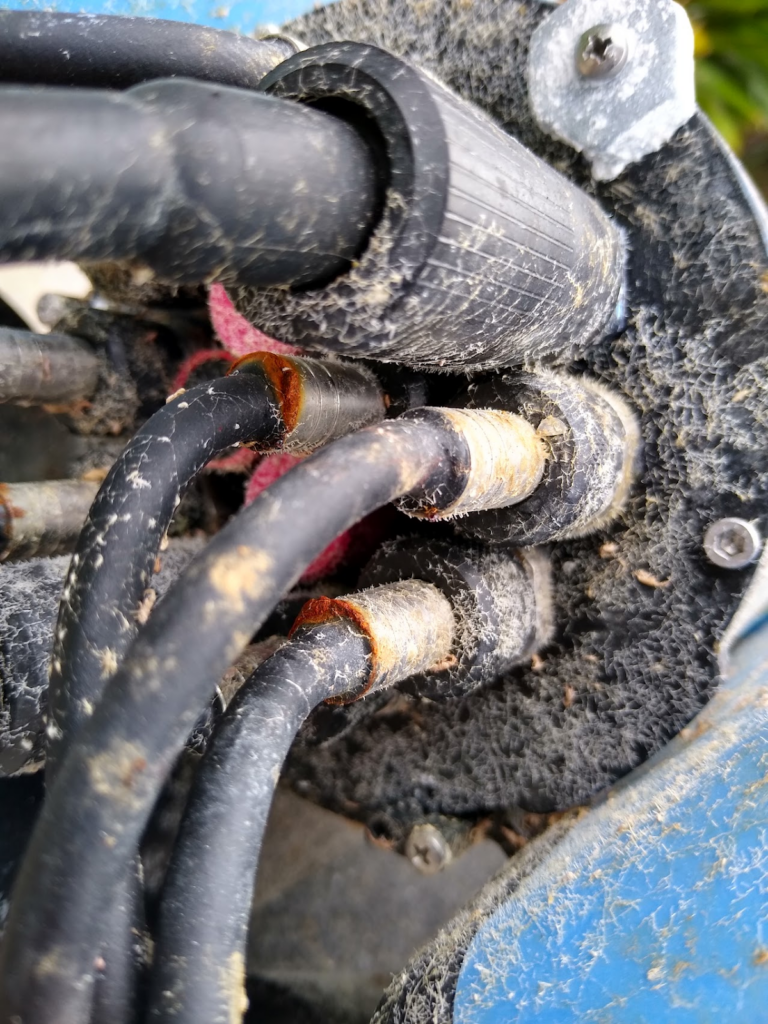
Zincs would typically last 8–10 months in 28–30 °C seawater, with no powdery residue from galvanic corrosion evident on disassembly. Bolted connections similarly are not at risk of stripping when removed, yet do not come loose from vibration (at least those present in a typical BlueROV2!)
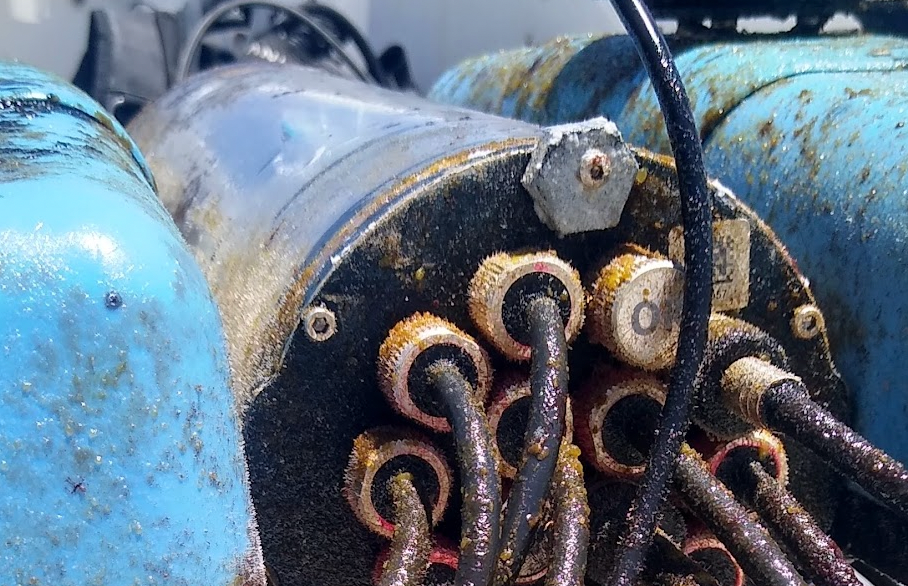
Resident ROVs can experience high current flow, which can increase the rate of corrosion! Using more than one zinc can help in these dynamic environments
Feedback
We’re always working to make our documentation, instructions, software, and user experience even better. If you have any ideas on how we can improve this guide, feel free to let us know here.